Mixing resin and hardener correctly is key to a successful epoxy project! Start by making sure you have safety gear like gloves and goggles, and a clean, ventilated workspace. Use a digital scale or graduated cylinders for precise measurements, typically a 2:1 ratio. Combine the parts in a clean container and mix slowly for at least three minutes, scraping the sides and bottom to guarantee thorough blending. A good resin choice depends on your project, and maintaining the right temperature is vital. Remember, patience during mixing pays off with a flawless finish. Get ready to discover more tips and tricks!
Key Takeaways
- Always measure resin and hardener precisely using calibrated tools to ensure correct ratios.
- Stir the resin and hardener mixture slowly for at least 3 minutes to avoid air bubbles.
- Use a clean, non-glass container for mixing to prevent contamination.
- Maintain a workspace temperature between 75-85°F (24-30°C) for optimal curing.
Safety and Equipment Preparation
Guaranteeing safety and proper equipment preparation is essential when handling resin and hardener. Start by gearing up with indispensable safety gear – eye protection and disposable latex or reusable rubber gloves are non-negotiable. These materials protect your skin and eyes from potential irritants and chemical splashes.
Next, let’s talk workspace setup. Your workspace should be well-ventilated to minimize fume exposure. Open windows, use fans, or even set up in an open garage to guarantee good airflow. A clean, organized workspace is critical, too. Confirm your mixing cups are spotless and free of any fats or oils, as contamination can ruin your mix.
Precision is key, so a small digital scale (down to 0.01 oz) or graduated cylinders are your best friends for accurate measurements. This precision guarantees you maintain the correct mix ratio, which is essential for proper curing.
Don’t forget to familiarize yourself with the technical data sheets specific to your epoxy system. These sheets hold important safe handling information and mixing guidelines. By adhering to these steps, you guarantee a safer and more effective mixing process, setting the stage for a successful project.
Selecting the Right Resin
When selecting the right resin, consider the specific needs of your project, such as whether you require a casting or coating resin, as each has unique properties and applications.
High viscosity resins are perfect for glossy finishes, while low viscosity options are better for deeper pours due to easier bubble release.
Additionally, always choose colorants formulated for epoxy resin and refer to manufacturer recommendations to guarantee compatibility and best results.
Resin Type Options
Selecting the right resin type is vital for achieving the best results in your specific project. Different resin types have unique properties and mixing ratios that make them suitable for various applications.
For instance, ArtResin is highly favored among artists due to its 1:1 mixing ratio, providing exceptional clarity and UV protection—perfect for preserving the beauty of artwork and decorative pieces.
On the other hand, epoxy coatings, which often require a 2:1 or 3:1 mixing ratio, are excellent for creating durable, protective finishes on surfaces like wood, concrete, and metal. These resins are designed to withstand wear and tear, making them ideal for high-traffic areas or functional items.
When it comes to selecting colorants for your resin, it’s important to choose ones specifically formulated for the resin type you are using. This guarantees they mix well without causing chemical reactions or inconsistencies.
Additionally, if your project calls for a glossy finish, high-viscosity resins are a great choice. For tasks where bubble release is a priority, lower-viscosity resins are more suitable. Understanding these factors will help you pick the perfect resin for your needs, securing a successful outcome.
Application Suitability
Choosing the appropriate resin for your project hinges on understanding the specific requirements and desired outcomes of the application. Different resin applications call for distinct types of resins, making project compatibility vital.
For example, casting resins are ideal for molded projects, offering the ability to capture fine details. On the other hand, if you’re aiming for a vibrant, tinted finish, you’ll want to use resin with compatible pigment paste or powder.
High viscosity resins are perfect for achieving glossy finishes, making them a great choice for projects where a shiny surface is desired. Conversely, lower viscosity resins are better for releasing bubbles, though they might compromise on the final surface appearance.
It’s also important to verify any colorants you use are specifically formulated for epoxy resin to avoid unwanted chemical reactions that could ruin your work.
Trusted suppliers like Just Resin offer materials known for their compatibility, helping you avoid issues during application and guaranteeing consistent results.
Whether your project involves art, repairs, or coatings, understanding the specific resin formulation optimized for your intended use will guide your selection process, assuring the best possible outcome.
Environmental Considerations
Understanding the environmental conditions, such as temperature and humidity, is essential in selecting the right resin for your project to guarantee ideal curing and final performance. Temperature fluctuations and humidity effects can greatly impact the resin’s behavior and the quality of the final product.
Ideal working conditions are typically between 75-85°F (24-30°C) with low humidity levels. Operating outside this range can lead to improper curing or even complete failure of the project.
Here’s what to keep in mind:
- Temperature fluctuations: Rapid changes can cause the resin to cure unevenly, resulting in a weak or brittle structure.
- Humidity effects: High humidity can introduce moisture into the resin mix, leading to cloudiness or improper bonding.
- Resin type: Choose between casting resins for molds and coating resins for surfaces, based on your application requirements.
Accurate Measuring Techniques
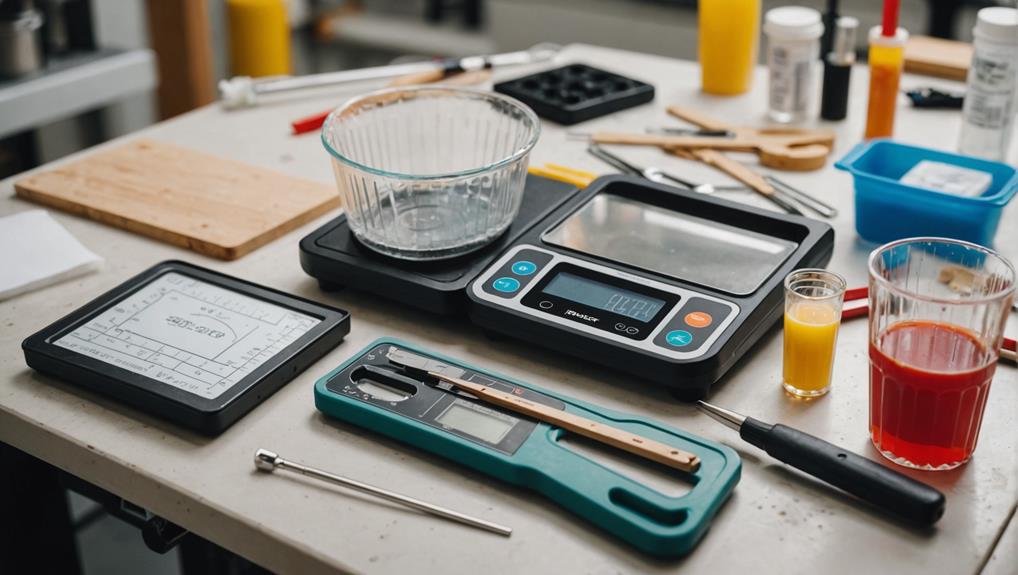
Accurate measurement of resin and hardener is essential to guarantee a proper mix and ideal curing of epoxy. Using calibrated tools is paramount in achieving measuring accuracy. A calibrated measuring cup can precisely measure the resin and hardener, assuring that you follow the recommended mixing ratio of 2 parts resin to 1 part hardener by volume. Before pouring in the resin, make sure to reset the scale to zero with the mixing cup in place, which avoids any discrepancies in weight measurements.
For the best results, always measure Part A (resin) and Part B (hardener) separately before combining them. This practice helps prevent waste and assures accurate ratios. When measuring by weight, a minimum of 1.47 oz of mixed epoxy is recommended to assure proper curing, with a 5% error margin allowed for hardener calculations. Additionally, verify the meniscus position when using graduated measuring cups for volume measurements; this assures precision in measuring the resin and hardener.
Here is a visual representation to aid in understanding:
Measurement Method | Tool Required | Key Consideration |
---|---|---|
Volume | Calibrated measuring cup | Meniscus position |
Weight | Digital scale | Reset scale to zero |
Mixing | Clean mixing cup | Measure separately first |
These steps will help achieve the right consistency and curing for your epoxy projects.
Weight Vs. Volume Measurement
When mixing resin and hardener, the choice between weight and volume measurement can greatly impact the accuracy and quality of the final product.
Weight measurement tends to be more accurate due to the varying densities of resin and hardener. For instance, a typical weight ratio for a two-part epoxy might be 100:47 (resin to hardener). This precision minimizes errors and guarantees a reliable mixture.
On the other hand, volume measurement is more straightforward but requires careful attention to detail. Using calibrated measuring cups, a common volume ratio for epoxy is 2 parts resin to 1 part hardener. This method demands that you check the fluid levels at the correct meniscus position for accuracy.
To help you choose between these methods, consider the following:
- Weight advantages: More precise, reduces errors due to density variations.
- Volume considerations: Easier and faster, but requires careful measuring.
- Practical example: For a 2:1 mix by volume, 4 oz of mixture needs 2.67 oz of resin and 1.33 oz of hardener by weight.
Understanding these aspects can greatly improve your resin projects.
Mixing Resin and Hardener
To achieve the best results, it is essential to measure and mix resin and hardener accurately according to the manufacturer’s specified ratio. Typically, this is 2 parts resin to 1 part hardener by weight or volume. Using clean, non-glass containers, such as disposable plastic cups, guarantees precise measurements and prevents contamination, which is critical for maintaining the desired resin consistency.
Once measured, combine the resin and hardener, stirring thoroughly for at least 3 minutes. Scrape the sides and bottom of the container to achieve a uniform consistency without hazy streaks. Maintaining a working temperature between 75-85°F (24-30°C) is imperative, as it affects the chemical reaction and curing process.
To minimize air bubbles, mix slowly and deliberately. If bubbles persist, consider using a vacuum chamber post-mixing.
Step | Description |
---|---|
1. Measure | Use the specified ratio (e.g., 2 parts resin to 1 part hardener) |
2. Combine | Pour resin and hardener into a clean, disposable plastic cup |
3. Stir | Mix thoroughly for at least 3 minutes, scraping sides and bottom |
4. Temperature | Maintain 75-85°F (24-30°C) for best results |
5. Air Bubbles | Mix slowly and use a vacuum chamber if necessary |
Proper Mixing Techniques
Thorough mixing of resin and hardener is essential to achieving a uniform, streak-free consistency important for ideal curing and finish. To avoid mixing errors, follow these precise steps to guarantee your final product is flawless.
First, measure your resin and hardener using a clean, calibrated mixing cup. For a typical 2:1 epoxy mix, combine 2 parts resin (Part A) with 1 part hardener (Part B). Accurate ratios are key to maintaining the correct resin viscosity and guaranteeing proper curing.
Stir the mixture slowly for at least 3 minutes, making sure to scrape the sides and bottom of the container. Slow stirring helps to minimize air bubbles, which can mar the final finish.
Here are some key points to remember:
- Use a timer to track the mixing duration; over-mixing generates excess heat, while under-mixing leads to tacky surfaces.
- Pour into a new container after mixing to avoid any unmixed resin clinging to the sides.
- Consider a vacuum chamber to effectively remove any air bubbles after mixing.
Application and Working Time
Effective application of mixed resin requires careful attention to its limited working time, typically between 35 to 45 minutes. This window is your golden hour when the resin remains workable, so you need to act fast and smart. Jump into action immediately after mixing, because the clock is ticking! Larger batches can heat up quicker, reducing your working time even more. Imagine trying to finish a puzzle as the pieces slowly freeze in place—that’s what you’re up against.
Now, let’s talk application techniques. During this “open time,” you can assemble parts, clamp them together, and guarantee everything aligns perfectly. Keep an eye on the resin as it shifts from a liquid to a gel. This is essential because you can still add more layers without extra prep if the surface is tacky. It’s like putting a sticker on a sticky note; perfect timing secures a strong bond.
Curing Processes and Phases
Now that you know how to mix resin and hardener, let’s talk about what happens next—the curing process.
This journey from liquid to solid involves three key phases: open time, initial cure, and final cure, each with its own vital role.
Temperature plays a big part too, as warmer conditions can speed things up, so keeping an eye on your workspace’s temperature is essential to get the best results.
Stages of Epoxy Curing
Understanding the stages of epoxy curing is essential for achieving ideal results in any resin application. The curing process progresses through three distinct phases: liquid, gel, and solid state. Each stage has unique characteristics that influence the final outcome of your project.
In the initial liquid phase, also known as the open time, the epoxy remains workable. This is the period when you can manipulate the mixture, make adjustments, and guarantee proper coverage.
As the epoxy continues to cure, it enters the gel phase. During this stage, the mixture begins to thicken and becomes tacky. This is a critical time for bonding other surfaces, as the epoxy is starting to set but is still flexible enough to form strong connections.
Finally, the epoxy reaches its solid state, achieving its full strength and durability. This final cure phase typically takes between 24 to 48 hours, depending on environmental conditions like temperature and humidity.
- Liquid Phase: Epoxy is fully workable and adjustable.
- Gel Phase: Epoxy thickens and becomes tacky, ideal for bonding.
- Solid State: Epoxy hardens, reaching full strength.
Understanding these stages guarantees a flawless finish for your epoxy projects.
Temperature’s Role in Curing
Temperature plays a pivotal role in the curing process of epoxy resin, greatly influencing the speed and quality of each phase. The temperature effects are quite noticeable; for instance, higher temperatures speed up the curing process due to the exothermic nature of the chemical reaction. This means your resin will move from liquid to gel to solid much faster, which sounds great, right?
Well, not always. While warmer conditions can shorten the overall cure time, making your project finish quicker, it also means you have less time to work with the resin before it starts to set. That’s where curing efficiency comes in. Ideally, you should maintain an ambient temperature between 75°F and 85°F (24°C to 30°C) for best results.
Using a slower hardener can help you manage the resin better in warm environments, giving you more time to perfect your work.
But be cautious—too much heat can cause thick epoxy masses to generate excessive heat, posing risks like burns or even ignition. So, always keep an eye on the temperature during the curing process to guarantee everything goes smoothly.
Surface Preparation for Bonding
Proper surface preparation is vital for achieving strong adhesion when applying epoxy resin, necessitating that surfaces be clean, dry, and textured. To guarantee ideal bonding, it’s essential to focus on surface cleaning and texture enhancement. Here’s how to get it right:
- Surface Cleaning: Use appropriate solvents to clean the surfaces, making sure they are free from dust, grease, and other contaminants. This step greatly enhances the strength of the bond.
- Texture Enhancement: Sand glossy areas with 80-grit sandpaper after cleaning. This creates a rough texture that promotes better mechanical bonding when applying fully cured epoxy.
- Removing Amine Blush: This wax-like film can inhibit bonding. Wash it away with water and abrasive pads before applying additional epoxy layers.
Preventing Adhesion Issues
Guaranteeing ideal adhesion begins with meticulously cleaning and preparing surfaces to be free of contaminants before applying epoxy. Surface contaminants, such as dirt, grease, and amine blush, can severely compromise bond strength, leading to adhesion challenges. Washing surfaces with clean water and abrasive pads will effectively remove amine blush. Additionally, sanding glossy, fully cured surfaces with 80-grit sandpaper can create a textured profile, enhancing mechanical bonding.
In cases where unwanted bonding might occur, applying clear tape, plastic, or mold release agents can be beneficial. Conducting adhesion tests on small, inconspicuous areas first guarantees the epoxy will bond correctly without compromising the entire project.
Here’s a quick reference table to guide you through the process:
Step | Action | Purpose |
---|---|---|
1. Cleaning | Wash with water and abrasive pads | Remove amine blush and contaminants |
2. Sanding | Use 80-grit sandpaper on cured surfaces | Enhance mechanical bonding |
3. Protection | Apply clear tape/plastic | Prevent unwanted adhesion |
4. Testing | Conduct adhesion tests on small areas | Verify bond strength |
5. Drying | Guarantee surfaces are dry and dust-free | Prevent delamination and adhesion issues |
Finishing and UV Protection
Achieving a smooth, glossy finish on epoxy resin projects not only enhances their aesthetic appeal but also contributes greatly to their durability. Proper finishing is vital, and incorporating UV protection is essential to prevent sunlight degradation. Here are some effective strategies to achieve this.
Finish Coatings: Applying two-part linear polyurethane paints offers a durable and UV-resistant finish, ideal for protecting cured epoxy surfaces.
UV Resistance: High-gloss white coatings provide the best longevity and resistance against yellowing, guaranteeing your project looks pristine for longer.
Post-Curing: Enhancing the thermal properties of epoxy through post-curing at raised temperatures can lead to improved performance and durability.
Moisture Sealing: A good finish coat seals the epoxy, preventing moisture penetration and further enhancing the longevity of your project.
Applying these techniques guarantees your epoxy resin projects not only look fantastic but also stand the test of time.
Remember, while the finish coatings add that final touch of brilliance, UV resistance is what keeps your hard work from turning into a yellowed disappointment.
Frequently Asked Questions
What Is the Proper Mixture of Resin and Hardener?
The proper mixture of resin and hardener varies by resin types, typically following specific mixing ratios. For instance, the Super SAP CLR epoxy system recommends a 2:1 ratio by weight or volume to guarantee ideal curing and performance.
How to Mix Resin Correctly?
To mix resin correctly, employ precise mixing techniques such as using calibrated measuring tools and thorough stirring. Common mistakes include inaccurate measurements and insufficient mixing, which can lead to improper curing and suboptimal performance of the final product.
Does Hardener or Resin Go First?
For ideal accuracy in measurements, it is generally advised to pour the resin first due to its viscosity. Different hardener types may affect mixing order, so always follow the manufacturer’s guidelines for specific recommendations.
Will Resin Harden Faster With More Hardener?
Increasing the amount of hardener does not expedite resin curing. Instead, it disrupts the chemical reaction, potentially causing uneven curing, excessive heat, and surface defects. Adherence to the recommended ratios is essential for ideal results.
Conclusion
In sum, achieving the best results when mixing resin and hardener requires meticulous attention to safety, precise measurement techniques, and thorough mixing processes.
Proper curing and surface preparation are essential to prevent adhesion issues and guarantee a strong bond.
Finally, finishing techniques and UV protection contribute to the durability and longevity of the resin application.
By following these steps, ideal performance and high-quality outcomes can be consistently achieved in resin-based projects.
Leave a Reply