Mastering resin 3D art starts with understanding how resin works and gathering essential tools like a resin printer and UV light. Choose the right type of resin for your project—standard for detailed models, tough for durability, or flexible for bendable pieces. Safety is key, so always use gloves, goggles, and work in a ventilated area. Next, design your model using software like Blender, preparing it meticulously before slicing and printing. Troubleshoot common issues like layer separation and bubbles by adjusting settings. Finally, post-process with cleaning, curing, and adding final touches. Stick around to reveal more secrets and tricks!
Key Takeaways
- Select the right type of resin for your project needs, considering durability, flexibility, and eco-friendliness.
- Use proper safety gear like gloves, goggles, and masks, and work in well-ventilated areas to avoid harmful fumes.
- Optimize your 3D model design by ensuring it is manifold, has appropriate wall thickness, and is hollowed with drainage holes.
- Prepare your resin printer by calibrating, cleaning the resin vat, and ensuring the UV light source is functional.
Understanding Resin 3D Art
Grasping the fundamentals of resin 3D art begins with comprehending the basic principles and materials involved in the process. Resin history dates back to ancient civilizations, where natural resins were used for crafting and preservation.
Today, we’ve come a long way, and resin 3D art is a modern marvel. It involves using liquid resin and a 3D printer to create intricate and detailed objects layer by layer. The magic happens when photopolymer resins cure under UV light, resulting in smooth finishes and vibrant colors.
Artistic techniques in resin 3D art are as varied as the artists themselves. Imagine creating prototypes for cool gadgets, detailed miniatures for your favorite board games, or even unique pieces of jewelry.
The precision of resin materials allows artists to capture the finest details, making their creations come to life. Depending on the project, artists choose from different types of resin. Standard resin is great for everyday projects, while tough resin handles more wear and tear. Flexible resin, on the other hand, bends without breaking—perfect for more dynamic designs.
Understanding the basics of resin 3D art opens up a world of creative possibilities, limited only by your imagination!
Essential Tools and Materials
Mastering resin 3D art necessitates the use of important tools and materials that guarantee precision, safety, and quality in every project. To get started, you’ll need a resin printer, which is the heart of your setup. This machine brings your digital designs to life. A UV light source is critical for curing, solidifying your creations with a magical touch. Mixing containers and stirring sticks are simple but essential tools to make sure your resin and hardener mix just right, avoiding any gooey disasters.
Don’t forget about personal protective equipment (PPE) like gloves, goggles, and masks. These are non-negotiable, as they protect you from the nasty fumes and potential skin irritations that come with working with resin. High-quality resin is another must-have. Different projects call for different types of resin—standard, tough, or flexible—so choose wisely based on your intended use. Resin suppliers often offer beginner kits, which are perfect for those just starting out.
Moreover, digital modeling software, like Blender or Tinkercad, is important for creating custom designs. Slicing software, such as ChiTuBox or Lychee, prepares your models for printing. Finally, regular maintenance tools keep your printer in top shape, making sure smooth, hassle-free printing.
Safety Precautions
While having the right tools and materials is fundamental, adhering to strict safety precautions is equally important when working with resin. Resin can be both amazing and hazardous, so taking the right steps to protect yourself is vital.
Here’s how to keep your resin art experience safe and enjoyable:
- Work in a well-ventilated area: This is non-negotiable. Resin releases fumes that can be harmful if inhaled. Make certain your workspace has good airflow, or use fans to keep the air moving.
- Wear safety equipment: Gloves, goggles, and masks are your best friends when working with resin. They protect your skin from contact, your eyes from splashes, and your lungs from fumes.
- Keep resin away from children and pets: Resin is not a toy. Store your materials and tools out of reach to prevent any accidental exposure or ingestion.
- Store properly: Keep your resin in a cool, dry place away from direct sunlight and heat sources. This helps maintain its stability and prevents premature curing.
Following these steps not only keeps you safe but also guarantees your art projects go smoothly. Remember, safety first means fun later!
Choosing the Right Resin
Choosing the right resin is like picking the perfect ingredient for a recipe; it makes all the difference.
You’ll want to think about what you’re creating—standard resin is great for detailed pieces, while tough and flexible resins are stronger and survive impacts.
Plus, don’t forget the environment; bio-based resins are becoming popular, helping reduce our footprint on the planet.
Resin Types Explained
Selecting the appropriate resin for your project is essential, as each type offers unique properties that can greatly influence the final outcome. Let’s explore the different types of resin and what makes each special.
First, we have epoxy resin, known for its strong adhesive properties and high gloss finish. The epoxy advantages include clarity and durability, making it perfect for intricate designs and durable art pieces. It’s like the superhero of resins, ready to save your project with its incredible strength and shine.
Next up is polyester resin. Often used in fiberglass applications, it’s a more cost-effective option for larger projects. While it might not provide the same level of detail as epoxy, it gets the job done without breaking the bank.
Then there’s polyurethane resin, which is flexible and resistant to abrasion. Polyurethane applications are ideal for projects requiring durability and impact resistance, like functional art pieces that need to withstand a bit of rough handling.
Finally, we have acrylic resin. This type offers a clear finish and is great for casting and surface coatings, giving your decorative objects a vibrant aesthetic.
Here’s a quick summary to help you pick:
- Epoxy Resin – Clarity and durability
- Polyester Resin – Cost-effective for large projects
- Polyurethane Resin – Flexibility and impact resistance
- Acrylic Resin – Clear and vibrant finish
Choosing the right resin is like picking the perfect tool for a job, ensuring your masterpiece turns out just the way you envisioned.
Application-Specific Choices
Determining the appropriate resin for your 3D printing project hinges on understanding the specific demands of the application, such as strength, flexibility, and the level of detail required. The application requirements dictate the material selection, so let’s break it down.
Standard resin is your go-to for high detail. It’s perfect for those intricate miniatures or detailed models where every tiny feature matters.
If your project needs to withstand some knocks, tough resin is the way to go. This material provides enhanced impact resistance, making it ideal for functional prototypes that need to survive real-world conditions.
For projects that need a bit of bendiness, like phone cases or wearable parts, flexible resin is your best friend. It stretches and bends without breaking, offering the durability and flexibility you need.
Then there’s castable resin, a superstar in the jewelry world. It’s designed for easy burnout, allowing for the creation of fine details and smooth surfaces in investment casting.
And don’t forget the most important step: ensuring the resin is compatible with your specific 3D printer model. Some printers have a picky appetite, only working well with certain resin types, so always double-check this before making your final material selection.
Environmental Considerations
Environmental sustainability significantly influences the selection of resin for 3D printing projects. When choosing resin, it’s important to reflect on how it impacts our planet. Many resins, like epoxy and polyester, can release harmful VOCs while curing, which makes good ventilation a must. But there are eco-friendly materials to evaluate that support sustainable practices.
Bio-based resins, derived from renewable resources, are a great option. They are greener alternatives to traditional petroleum-based resins. However, it’s essential to know how to dispose of them properly. Improper disposal can cause environmental damage and health risks, so always check the regulations.
Here are some things to keep in mind:
- Choose bio-based resins – They’re made from renewable resources and are kinder to the environment.
- Research disposal methods – Make sure you’re not harming the planet by throwing out resin incorrectly.
- Opt for low toxicity – Pick resins with low toxicity ratings and those that meet safety standards.
- Energy consumption – Be aware of the curing conditions, as some resins require more energy, affecting their environmental footprint.
Designing Your Model
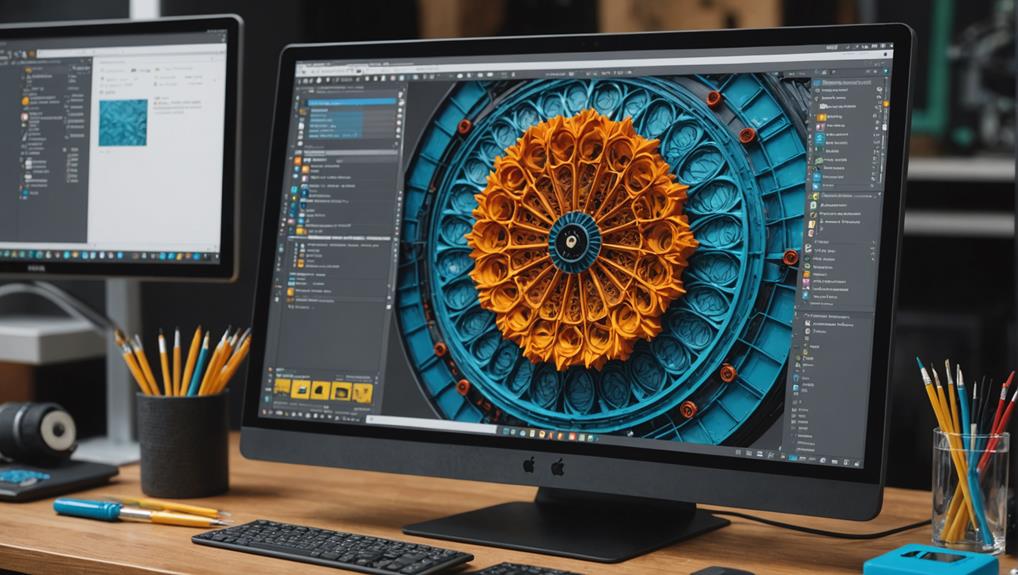
When designing your model for resin 3D printing, start by choosing user-friendly software like Blender or Tinkercad to create or tweak your designs.
Next, verify your model’s geometry is optimized to avoid printing errors—check for things like non-manifold edges and make sure it’s watertight.
Choosing Modeling Software
Selecting the appropriate modeling software is an essential first step in designing your 3D model for resin printing. The choice of software can greatly impact your creative process and the final outcome. Blender and Tinkercad are two popular options, each offering unique benefits and tools.
Blender features an extensive range of tools and flexibility, making it perfect for more complex and detailed designs. Tinkercad’s advantages include its beginner-friendly interface and web-based platform, which make it accessible and easy to learn. However, no matter which software you choose, it’s important to make sure it supports common file formats like STL and OBJ, fundamental for slicing and printing.
To help you decide, consider these four key points:
- Blender’s robust toolset: Perfect for advanced users who need a wide range of customization options.
- Tinkercad’s simplicity: Ideal for beginners or those looking for a quick, easy-to-use solution.
- Error-checking tools: Look for features that help identify and fix modeling errors, such as non-manifold edges.
- Scaling techniques: Make sure your software offers intuitive ways to resize your model to match your print requirements.
Don’t forget to explore community resources for tutorials and troubleshooting tips. Happy modeling!
Optimizing Model Geometry
Having chosen the right modeling software, the next step involves optimizing your model geometry to guarantee successful resin printing.
Start by ensuring your 3D model is manifold, meaning it has a closed volume with no pesky holes or non-manifold edges. Think of it like making sure your balloon has no leaks before inflating it!
Next, focus on mesh optimization to create a geometric efficiency. This means using the least amount of material while keeping your model strong. Aim for a wall thickness of 1-2 mm to prevent your print from collapsing. It’s like choosing the perfect balance between a sturdy castle wall and a delicate paper-thin sheet.
To save on resin and lighten your model, consider hollowing it out. But don’t forget to add drainage holes so the excess resin can escape, or you might end up with a gooey mess inside!
Also, orient your model strategically to minimize the need for support structures, making the post-processing less of a headache.
Preparing for Slicing
To guarantee a successful resin print, begin by meticulously designing your model with software such as Blender or Tinkercad, verifying its manifold status and correcting any common errors. This step is essential to make certain your model is ready for slicing without any hiccups.
Once your design is complete, save it in a compatible file format like STL or OBJ. These formats are universally accepted by slicing software, making the next steps smooth.
Before diving into slicing techniques, scale your model to the desired dimensions. Scaling affects print time and material usage, so get it right!
Next, open your slicing software, like ChiTuBox or Lychee, and set your layer settings. Layer thickness and exposure settings are vital for achieving that perfect print quality everyone admires.
Here’s a quick checklist to keep you on track:
- Check for Non-Manifold Edges: Fix any gaps or overlaps that can mess up your print.
- Save in STL or OBJ Format: Make sure your design file is compatible with slicing software.
- Scale Your Model: Adjust dimensions for the best print time and material use.
- Set Layer Thickness and Exposure: Fine-tune these settings for the highest print quality.
Preparing the Printer
Making sure that your 3D printer is properly set up is crucial for achieving high-quality resin prints. Start by placing your printer on a stable surface; vibrations can mess up your print quality and accuracy. Next, immerse yourself in printer calibration. You must level the build plate according to the instructions from your printer’s manufacturer—this guarantees that your prints stick well and don’t turn into a gooey mess.
Here’s a quick checklist:
Task | Why It Matters | Pro Tips |
---|---|---|
Surface Stability | Reduces vibrations | Use a sturdy table or desk |
Printer Calibration | Guarantees proper adhesion | Follow manual for precise leveling |
Clean Resin Vat & Plate | Prevents contamination | Regularly clean with isopropyl alcohol |
Now, let’s talk settings. Configuring your printer settings like layer height and exposure time is super crucial. These settings depend on your resin type and model requirements. Regularly cleaning the resin vat and build plate is another must-do to avoid any nasty surprises during printing. And don’t forget to check your UV light source—if it’s not working, your prints won’t cure properly and will stay gooey and sticky.
Follow these steps religiously, and you’ll be well on your way to creating stunning resin prints that look like they came straight out of a professional studio!
Slicing the Model
Slicing a 3D model is the transformative process of converting a digital design into a series of printable layers that your resin printer can accurately interpret. This step is vital! Without it, your printer wouldn’t know how to bring your creation to life.
Let’s explore the essentials of slicing settings and support structures.
Firstly, you’ll need slicing software like ChiTuBox or Lychee. These programs help you adjust settings such as layer thickness and exposure time. Proper slicing settings guarantee your model prints with the best quality and strength.
Next, always check for errors in your model. Non-manifold edges can cause print failures, but don’t worry, most slicing software can identify and fix these issues for you.
Support structures are another key element. They are especially important for complex models with overhangs. Supports stabilize these overhangs and prevent sagging or collapsing during the print.
Lastly, preview your sliced model. This step allows you to see the print layers and spot potential issues before initiating the print. Trust us, it’s better to find problems now rather than halfway through printing!
Here’s a quick recap:
- Choose reliable slicing software.
- Set your slicing settings accurately.
- Add necessary support structures.
- Preview your model thoroughly.
Happy slicing!
Initiating the Print
Initiating the print process requires meticulous calibration of the printer, particularly the Z-axis, to confirm ideal adherence of the initial layer to the build plate. This step is vital; imagine starting a race tied to a tree—you’re not going anywhere! Validating proper calibration means your first layer sticks firmly, setting the stage for a successful print.
Before you plunge in, check your print settings, especially the UV power settings. This guarantees the resin cures just right. Load your sliced model onto the printer, double-checking that settings like layer height and exposure time are dialed in for the resin you’re using. These settings are the secret sauce to strong layer adhesion and a smooth finish.
Once everything looks good, start the print and keep an eagle eye on those first few layers. This is where potential issues like poor adhesion or uneven curing might pop up. It’s like baking a cake—you don’t want it to flop right out of the oven!
Lastly, maintain a consistent ambient temperature. Resin is picky; it needs the right environment to flow and cure correctly. Think of it like Goldilocks—everything has to be just right for that perfect print.
Troubleshooting Print Issues
When it comes to mastering resin 3D art, troubleshooting print issues is essential.
Common problems like layer separation, bubbles, and adhesion issues can often be fixed by adjusting exposure settings and making sure your build plate is clean and level.
Let’s also consider how temperature and regular printer maintenance can play a big role in preventing print failures.
Common Print Failures
Understanding the intricacies of common print failures is essential for mastering resin 3D art and achieving consistently high-quality results.
One major issue is layer separation. This happens when layers don’t stick together properly, often due to improper exposure settings or poor build plate adhesion. Imagine spending hours on a cool dragon model, only to find its wings falling apart—that’s layer separation in action!
Another pesky problem is print warping. If the ambient temperature isn’t stable, your masterpiece might end up looking like it was left in a hot car. Keeping the printing environment steady is vital for resin viscosity and overall print quality.
Here are some common print failures that can really mess up your day:
- Bubbles in Prints: These little annoyances come from trapped air during mixing. Thoroughly mix your resin to keep your prints smooth.
- Incorrect Model Orientation: Placing your model at the wrong angle can cause failures. Orient models to reduce support and improve layer adhesion.
- Layer Separation: We can’t stress this enough! Proper settings and good adhesion are your best friends.
- Print Warping: Maintain a stable temperature to avoid unexpected distortions.
Regular maintenance, like cleaning the build plate and checking the UV light source, also goes a long way in preventing these issues.
Resolving Adhesion Problems
Proper adhesion is fundamental to successful resin 3D printing, and addressing adhesion issues involves meticulous attention to build plate preparation, resin selection, and printer settings. Imagine you’re baking cookies, and the dough just won’t stick to the tray—frustrating, right? Well, the same goes for resin 3D printing. If the print surface isn’t cooperating, your masterpiece might end up a messy blob.
First, make sure your build plate is leveled and spotless. Any dust or grease can act like a slippery banana peel for your resin.
Next, think about using a high-quality print surface like glass or a textured plate. These surfaces can give your prints a better grip, much like sandpaper helps your shoes stick on a slick floor.
Another trick is tweaking the exposure time for the first few layers. A bit more light can give your resin a firmer hold. You can also try a thin layer of adhesive—think of it as adding sticky tape to help things stay put.
Post-Processing Techniques
Effective post-processing techniques are vital for achieving high-quality results in resin 3D art. Once your masterpiece is off the build plate, it’s time to make it shine.
First, cleaning techniques are important. Use isopropyl alcohol (IPA 99.9%) right away to remove any uncured resin. Trust me, you don’t want sticky residue ruining your hard work.
Next, let’s talk about curing methods. Curing your prints under UV light is a must for durability. A dedicated curing chamber guarantees each inch is evenly exposed, giving your art the strength it needs.
Here are four key steps to master post-processing:
- Immediate Cleaning: Dip your print in IPA 99.9% to wash away uncured resin, guaranteeing a smooth finish.
- UV Curing: Use a UV curing chamber to harden your print completely, making it robust and ready for the next steps.
- Sanding: Carefully sand with fine-grit sandpaper. Be gentle, especially around intricate details, to avoid damage.
- Hot Sculpting: Use heated tools to fill small imperfections. This step repairs and perfects your piece before final curing.
Adding Finishing Touches
Applying the finishing touches to your resin 3D art raises it from a mere creation to a polished, professional piece.
Start by thoroughly cleaning your resin art with isopropyl alcohol (IPA 99.9%) to remove any uncured resin. This step is essential for a smooth finish. Next, cure your prints under UV light, making sure all surfaces are evenly exposed. This guarantees your piece is strong and durable.
Now, let’s talk about sanding. Begin with a coarser grit of sandpaper to smooth out the larger imperfections. Gradually move to finer grits, which will refine the surface and prepare it for additional treatments. This step might seem tedious, but trust me, it’s worth it.
For an extra touch of elegance, consider surface treatments like a clear epoxy resin coat. This not only gives your piece a stunning gloss but also protects it from scratches and UV damage.
Want to add some color? Acrylic paints and metallic finishes can make your art pop. Just make certain the surface is clean before you start painting.
These finishing techniques will transform your resin 3D art, making it a standout piece that everyone will admire.
Tips for Improvement
Enhancing the quality and precision of your resin 3D prints requires a combination of meticulous calibration, high-quality materials, and ongoing maintenance practices. Achieving print consistency and resin durability involves paying attention to the finer details and making informed choices.
- Calibrate Regularly: Regular calibration is key. It guarantees consistent layer adhesion and prevents misalignment. Think of it as tuning a musical instrument; without it, your prints might hit a sour note.
- Choose Quality Resins: Not all resins are created equal. High-quality resins tailored to your project’s needs can make a world of difference in durability, detail, and finish. It’s like picking the right paint for a masterpiece.
- Experiment with Settings: Don’t be afraid to tweak exposure times and layer heights. These adjustments can optimize print quality and reduce errors. It’s a bit like adjusting the recipe until your cookies are just right.
- Maintain Your Printer: Clean your build plate and replace worn components regularly. These practices prolong your printer’s life and enhance print outcomes. Think of it as giving your printer a spa day—it’ll thank you with better prints.
Engage with online communities to share experiences and gather new techniques, enriching your skills and knowledge in resin 3D printing.
Frequently Asked Questions
How to Use Resin in Art Step by Step?
To use resin in art, first select the appropriate resin type. Ascertain resin safety by working in a well-ventilated area. Measure and mix resin accurately, incorporate color mixing, pour into molds, and allow curing for 24-72 hours.
What Is the Best Ratio for Resin Art?
The best ratio for resin art depends on the resin types used, typically ranging from 1:1 to 2:1 (resin to hardener). Accurate measurement and mindful color mixing, not exceeding 10%, are essential for ideal curing.
Is Artresin Self Leveling?
Yes, ArtResin possesses self leveling properties that enhance the resin surface finish. When poured at the recommended temperature and mixed correctly, it spreads evenly to create a smooth, glass-like finish, free of imperfections.
How Do You Mix Artresin and Hardener?
To mix ArtResin and hardener, employ precise mixing techniques, using a 1:1 ratio by volume. Stir for 3 minutes, ensuring thorough blending. Follow safety precautions, such as wearing gloves and working in a well-ventilated area.
Conclusion
In conclusion, mastering resin 3D art requires understanding the fundamentals, gathering essential tools, and prioritizing safety.
Choosing the right resin and designing a solid model are vital steps.
Addressing print issues and employing effective post-processing techniques enhance the final product.
Adding finishing touches and continually seeking improvement raise the artistry.
By following these steps, one can develop proficiency in resin 3D art and create impressive and detailed works.
Leave a Reply